The Airbus A350 is a wide-body airliner that has redefined long-haul flights. Combining cutting-edge materials, advanced aerodynamics, and modern engines, the A350 delivers operational efficiency that leaves aviators in awe.
From Challenge to Triumph
The story of the Airbus A350 didn’t start from scratch – it began with a tough challenge. In 2004, Boeing unveiled its 787 Dreamliner, promising a revolution in fuel efficiency and comfort. Airbus, then a market leader with the A330, initially brushed it off: "Just a response to our success, no big deal." But airlines grew restless – Boeing boasted 20% fuel savings, and the A330 started looking dated. Pressured by customers, Airbus revealed a first sketch in September 2004: the A350 as an upgraded A330 with new wings, engines, and composites. The idea was simple – take a proven fuselage and modernize it.
The market, however, said "no." Big potential buyers like Qatar Airways and Singapore Airlines slammed the project: too similar to the A330, not ambitious enough. Airbus realized half-measures wouldn’t cut it and in 2006 launched a bold new plan – the A350 XWB (eXtra Wide Body). This wasn’t an upgrade; it was a clean slate: a wider fuselage, more composites (52% of the structure), new Rolls-Royce Trent XWB engines, and wings with state-of-the-art aerodynamics. The budget ballooned to 11 billion euros, but it was worth it – the A350 was set to rival not just the 787 but also the Boeing 777.
Development moved at a relentless pace. In December 2008, the design was frozen at Maturity Gate 5 (the point where engineers say, "It works, let’s build it"), and in December 2012, the first prototype, MSN1, rolled out of the Toulouse hangar. On June 14, 2013, the A350-900 took flight – pilots Carlos Cruz and Peter Chandler flew it over France for four hours. EASA certification arrived on September 30, 2014, followed by FAA approval two months later. Qatar Airways, the launch customer, received its first aircraft on December 22, 2014, and on January 15, 2015, the A350 carried passengers from Doha to Frankfurt.
From the 2006 concept to its 2015 debut, it took nearly a decade. The A350 XWB became Airbus’s answer to the times – a plane that didn’t just catch up to competitors but set new benchmarks in efficiency, comfort, and technology. Let’s break down what makes this bird soar on ultra-long journeys.
From Challenge to Triumph
The story of the Airbus A350 didn’t start from scratch – it began with a tough challenge. In 2004, Boeing unveiled its 787 Dreamliner, promising a revolution in fuel efficiency and comfort. Airbus, then a market leader with the A330, initially brushed it off: "Just a response to our success, no big deal." But airlines grew restless – Boeing boasted 20% fuel savings, and the A330 started looking dated. Pressured by customers, Airbus revealed a first sketch in September 2004: the A350 as an upgraded A330 with new wings, engines, and composites. The idea was simple – take a proven fuselage and modernize it.
The market, however, said "no." Big potential buyers like Qatar Airways and Singapore Airlines slammed the project: too similar to the A330, not ambitious enough. Airbus realized half-measures wouldn’t cut it and in 2006 launched a bold new plan – the A350 XWB (eXtra Wide Body). This wasn’t an upgrade; it was a clean slate: a wider fuselage, more composites (52% of the structure), new Rolls-Royce Trent XWB engines, and wings with state-of-the-art aerodynamics. The budget ballooned to 11 billion euros, but it was worth it – the A350 was set to rival not just the 787 but also the Boeing 777.
Development moved at a relentless pace. In December 2008, the design was frozen at Maturity Gate 5 (the point where engineers say, "It works, let’s build it"), and in December 2012, the first prototype, MSN1, rolled out of the Toulouse hangar. On June 14, 2013, the A350-900 took flight – pilots Carlos Cruz and Peter Chandler flew it over France for four hours. EASA certification arrived on September 30, 2014, followed by FAA approval two months later. Qatar Airways, the launch customer, received its first aircraft on December 22, 2014, and on January 15, 2015, the A350 carried passengers from Doha to Frankfurt.
From the 2006 concept to its 2015 debut, it took nearly a decade. The A350 XWB became Airbus’s answer to the times – a plane that didn’t just catch up to competitors but set new benchmarks in efficiency, comfort, and technology. Let’s break down what makes this bird soar on ultra-long journeys.
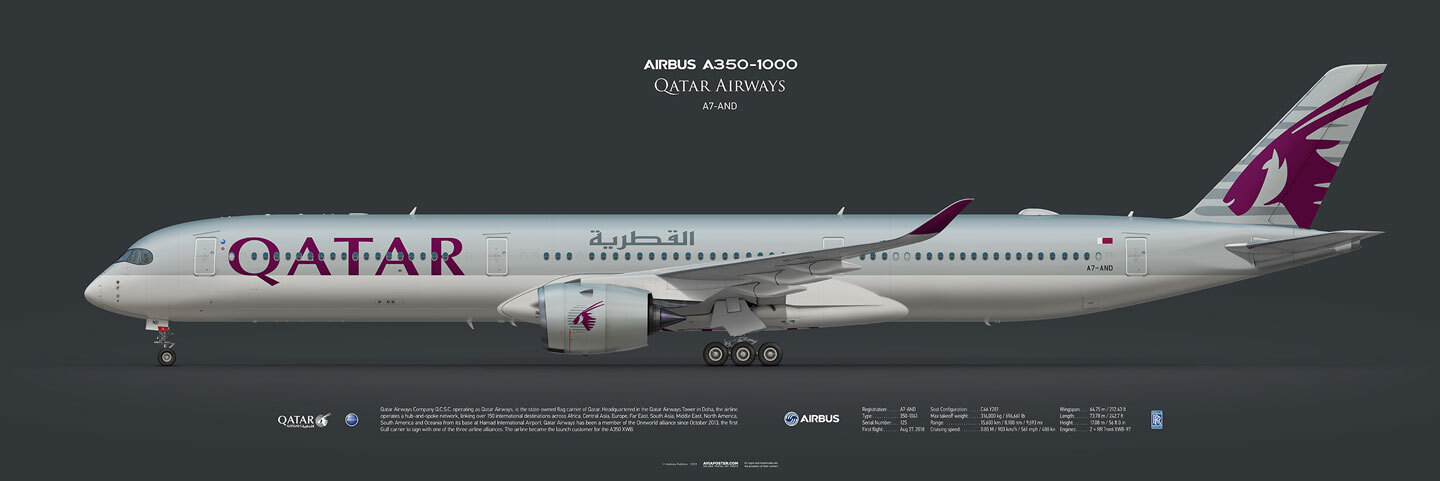
Fuselage: Wider and Lighter
The Airbus A350 XWB’s fuselage isn’t just a "tube with seats" – it’s a smart design that boosts comfort, strength, and economy. At 5.96 meters in diameter (XWB stands for eXtra Wide Body), it’s 13 cm wider than the Boeing 787 and 33 cm wider than the A330. Those extra centimeters aren’t just numbers – they mean more shoulder room, wider aisles, and the ability to fit nine seats per row in economy (with two aisles) without feeling like "sardines in a can."
The big surprise? Materials. Over 70% of its structure uses advanced stuff: 53% is carbon-fiber-reinforced polymer (CFRP) – a composite of carbon fibers and polymer resin, usually epoxy – 14% is titanium, and the rest includes various aluminum-lithium alloys. What’s the payoff? CFRP’s strength-to-weight ratio beats traditional aluminum, cutting weight while keeping rigidity. The fuselage panels, wings, and even parts of the tail are made of carbon fiber, assembled with precision to handle loads up to 1.5 times the maximum expected in flight. Aluminum-lithium alloys, with lower density and high crack resistance, get an extra boost from scandium doping, enhancing strength and weldability. The result? A lighter plane – about 20% lighter than a comparable aluminum airframe – directly boosting fuel savings, range, and payload.
Airbus adopted "panel construction" for the fuselage. It’s built from large composite panels (up to 19 meters long) rather than tons of small sheets like in the old days. This speeds up production and cuts down on seams, making it stronger and more airtight. The panels link to a frame of 84 ribs (on the A350-900), some of which are composite too. These ribs aren’t just bolted – they’re joined with friction stir welding (FSW). Here’s how it works: a spinning tool generates heat through friction, softening the material (without melting it), then "stirs" it into a solid seam. It’s cool because the weld is nearly flawless, lighter than traditional methods, and skips extra bolts or rivets, trimming weight. Airbus uses this to make the fuselage tougher and tighter.
The fuselage shape is clever too. It’s not perfectly round but slightly oval in cross-section, with a flatter bottom. This improves aerodynamics and adds space in the cargo hold.
Windows got bigger too – 11% larger than the A330’s, which were already decent for their time. On the A350, they’re about 41 cm tall and 28 cm wide, letting in more natural light and lifting passenger vibes. Plus, they’re positioned higher relative to the cabin floor, so even aisle-seat passengers can catch a glimpse of the sky or horizon. It’s a small touch that makes long flights nicer, especially for those not by the window. The glass? Composite too, with UV protection.
The fuselage faced brutal tests. In 2013, a test model endured 2.5 times normal pressure, and in 2014, it survived a simulated bird strike at 300 km/h. The verdict: it’s ready for loads up to 150% of normal. For passengers, there’s a bonus – cabin pressure mimics 1,800 meters altitude (versus 2,400 meters in older models), easing fatigue on long hauls.
Production happens mostly in France (Saint-Nazaire and Nantes), with final assembly in Toulouse. Over 10 years of service (2015–2025), the A350’s fuselage has proven it’s a blend of tech and comfort. No wonder Qatar Airways, the first buyer, called it "the future of aviation."
The Airbus A350 XWB’s fuselage isn’t just a "tube with seats" – it’s a smart design that boosts comfort, strength, and economy. At 5.96 meters in diameter (XWB stands for eXtra Wide Body), it’s 13 cm wider than the Boeing 787 and 33 cm wider than the A330. Those extra centimeters aren’t just numbers – they mean more shoulder room, wider aisles, and the ability to fit nine seats per row in economy (with two aisles) without feeling like "sardines in a can."
The big surprise? Materials. Over 70% of its structure uses advanced stuff: 53% is carbon-fiber-reinforced polymer (CFRP) – a composite of carbon fibers and polymer resin, usually epoxy – 14% is titanium, and the rest includes various aluminum-lithium alloys. What’s the payoff? CFRP’s strength-to-weight ratio beats traditional aluminum, cutting weight while keeping rigidity. The fuselage panels, wings, and even parts of the tail are made of carbon fiber, assembled with precision to handle loads up to 1.5 times the maximum expected in flight. Aluminum-lithium alloys, with lower density and high crack resistance, get an extra boost from scandium doping, enhancing strength and weldability. The result? A lighter plane – about 20% lighter than a comparable aluminum airframe – directly boosting fuel savings, range, and payload.
Airbus adopted "panel construction" for the fuselage. It’s built from large composite panels (up to 19 meters long) rather than tons of small sheets like in the old days. This speeds up production and cuts down on seams, making it stronger and more airtight. The panels link to a frame of 84 ribs (on the A350-900), some of which are composite too. These ribs aren’t just bolted – they’re joined with friction stir welding (FSW). Here’s how it works: a spinning tool generates heat through friction, softening the material (without melting it), then "stirs" it into a solid seam. It’s cool because the weld is nearly flawless, lighter than traditional methods, and skips extra bolts or rivets, trimming weight. Airbus uses this to make the fuselage tougher and tighter.
The fuselage shape is clever too. It’s not perfectly round but slightly oval in cross-section, with a flatter bottom. This improves aerodynamics and adds space in the cargo hold.
Windows got bigger too – 11% larger than the A330’s, which were already decent for their time. On the A350, they’re about 41 cm tall and 28 cm wide, letting in more natural light and lifting passenger vibes. Plus, they’re positioned higher relative to the cabin floor, so even aisle-seat passengers can catch a glimpse of the sky or horizon. It’s a small touch that makes long flights nicer, especially for those not by the window. The glass? Composite too, with UV protection.
The fuselage faced brutal tests. In 2013, a test model endured 2.5 times normal pressure, and in 2014, it survived a simulated bird strike at 300 km/h. The verdict: it’s ready for loads up to 150% of normal. For passengers, there’s a bonus – cabin pressure mimics 1,800 meters altitude (versus 2,400 meters in older models), easing fatigue on long hauls.
Production happens mostly in France (Saint-Nazaire and Nantes), with final assembly in Toulouse. Over 10 years of service (2015–2025), the A350’s fuselage has proven it’s a blend of tech and comfort. No wonder Qatar Airways, the first buyer, called it "the future of aviation."
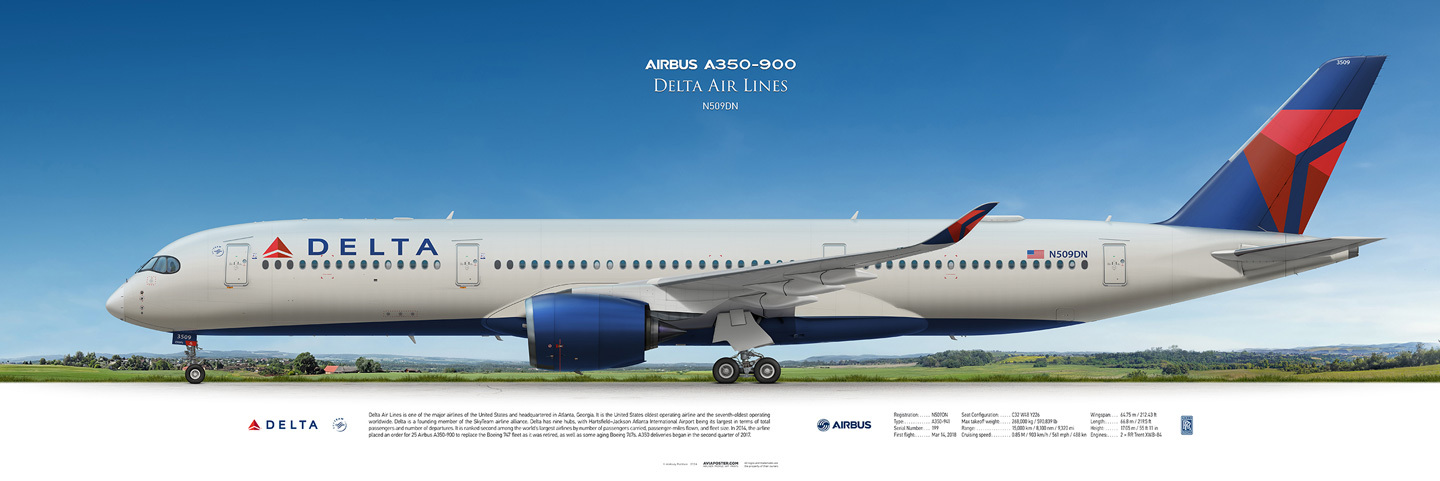
Unique Wings
Built at Airbus’s Broughton plant in the UK – in a new facility backed by the Welsh government – the A350’s wings are a true engineering marvel. With an aspect ratio of about 9.5:1, they strike a balance between long-range efficiency and practical design. It’s no fluke that the A350-900 can cover up to 8,300 nautical miles (and the A350-1000 up to 8,700). That range comes from meticulous aerodynamic work, validated by wind tunnel tests and computational fluid dynamics (CFD) during development.
The wings are adaptive, thanks to a curvature control system that adjusts flaps and slats in real time via onboard flight computers. This tweaks the wing’s shape mid-flight based on speed, altitude, and load, boosting efficiency at cruising speeds of Mach 0.85–0.89.
The wings don’t just lift the plane – they anchor it on the ground too. Airbus revamped the landing gear attachment for the A350 due to the composite wing structure. Traditionally, gear bolted to metal wings via reinforced nodes spread loads evenly. But carbon fiber, though strong and light, behaves differently – it’s less pliable than aluminum, and stresses distribute uniquely.
For the A350, Airbus crafted a "hybrid architecture" attachment system. Instead of bulky metal fittings that could crack the composite under stress, it uses spread-out anchor points. This cuts the risk of damage. The setup blends titanium and composite elements in the joints, preserving carbon fiber’s weight perks while ensuring durability.
Wingtip Concept
A quick glance at the A350 reveals its striking wingtips. These blended winglets curve upward and backward, seamlessly integrated into the wing – not bolted-on extras like on some planes, making them stand out from traditional designs.
Their main job? Cutting induced drag from wingtip vortices, boosting fuel efficiency and range – crucial for a plane pitched against the Boeing 787 and 777.
The A350’s wing spans 64.75 meters, with the final 4.4 meters forming those curved wingtips. This design locked in at Maturity Gate 5 after over 4,000 hours of wind tunnel tests and CFD modeling.
Built at Airbus’s Broughton plant in the UK – in a new facility backed by the Welsh government – the A350’s wings are a true engineering marvel. With an aspect ratio of about 9.5:1, they strike a balance between long-range efficiency and practical design. It’s no fluke that the A350-900 can cover up to 8,300 nautical miles (and the A350-1000 up to 8,700). That range comes from meticulous aerodynamic work, validated by wind tunnel tests and computational fluid dynamics (CFD) during development.
The wings are adaptive, thanks to a curvature control system that adjusts flaps and slats in real time via onboard flight computers. This tweaks the wing’s shape mid-flight based on speed, altitude, and load, boosting efficiency at cruising speeds of Mach 0.85–0.89.
The wings don’t just lift the plane – they anchor it on the ground too. Airbus revamped the landing gear attachment for the A350 due to the composite wing structure. Traditionally, gear bolted to metal wings via reinforced nodes spread loads evenly. But carbon fiber, though strong and light, behaves differently – it’s less pliable than aluminum, and stresses distribute uniquely.
For the A350, Airbus crafted a "hybrid architecture" attachment system. Instead of bulky metal fittings that could crack the composite under stress, it uses spread-out anchor points. This cuts the risk of damage. The setup blends titanium and composite elements in the joints, preserving carbon fiber’s weight perks while ensuring durability.
Wingtip Concept
A quick glance at the A350 reveals its striking wingtips. These blended winglets curve upward and backward, seamlessly integrated into the wing – not bolted-on extras like on some planes, making them stand out from traditional designs.
Their main job? Cutting induced drag from wingtip vortices, boosting fuel efficiency and range – crucial for a plane pitched against the Boeing 787 and 777.
The A350’s wing spans 64.75 meters, with the final 4.4 meters forming those curved wingtips. This design locked in at Maturity Gate 5 after over 4,000 hours of wind tunnel tests and CFD modeling.
Post-certification, Airbus flew MSN003 with one wingtip removed to test the plane’s behavior in odd conditions.
The A350 first flew in 2013, but by 2017, Airbus was testing a taller, squarer wingtip design. It debuted on prototype MSN001 and rolled out officially with MSN216 – the first A350-900ULR for Singapore Airlines. Paired with a wing twist tweak to optimize lift distribution, it cut drag further. Experts say it added about 100 nautical miles (185 km) to the A350-900’s range and 140 miles (259 km) to the A350-1000’s. The updated wingtips became standard from MSN216 onward, though earlier models (MSN215 and below) kept the original shape.
Rolls-Royce Trent XWB Engines: The Heart of the A350
The Airbus A350 wouldn’t be what it is without its Rolls-Royce Trent XWB engines. These turbofans, built just for the A350 family, rank among the world’s most efficient. The Trent XWB isn’t just another engine – it’s the sixth in the storied Trent lineup, proven on planes like the Boeing 787 (Trent 1000) and Airbus A380 (Trent 900).
Rolls-Royce offers two variants: the Trent XWB-84 with 84,200 pounds of thrust (375 kN) for the A350-900, and the beefier Trent XWB-97 with 97,000 pounds (431 kN) for the A350-1000 and freighter A350F. Both stick to Trent’s signature three-shaft design – separate shafts for the fan, intermediate compressor, and high-pressure compressor. Each spins at its ideal speed, avoiding extra strain. This trims the size and weight of parts, and with new alloys, sheds dozens of kilograms. Plus, the tailored speeds (slower fan, faster high-pressure compressor) cut vibrations, making the setup more stable.
Development kicked off in 2006 when Airbus tapped Rolls-Royce as the sole engine supplier. The first run fired up on June 14, 2010, and the A350’s maiden flight came on June 14, 2013. Since then, the Trent XWB has logged over 15 million flight hours (as of March 2024) with a stellar 99.9% reliability rate. Its 3-meter fan, 9.6:1 bypass ratio, and 50:1 pressure ratio let it gulp more air and burn less fuel – 15% better than the first-gen Trent.
It wasn’t all smooth sailing. In 2018, a Trent XWB-97 failed mid-flight due to blade wear, and in 2024, Cathay Pacific hit a fire from a busted fuel line. Rolls-Royce jumped on fixes, boosting durability for hot, sandy spots like the Emirates. Today, it’s evolving – in December 2024, an upgraded XWB-84 got certified with even lower fuel burn.
The Trent XWB powers the A350’s heart, thumping through 20-hour Qantas flights from Sydney to London. Oh, and it’s the best-selling Trent ever – over 1,600 orders!
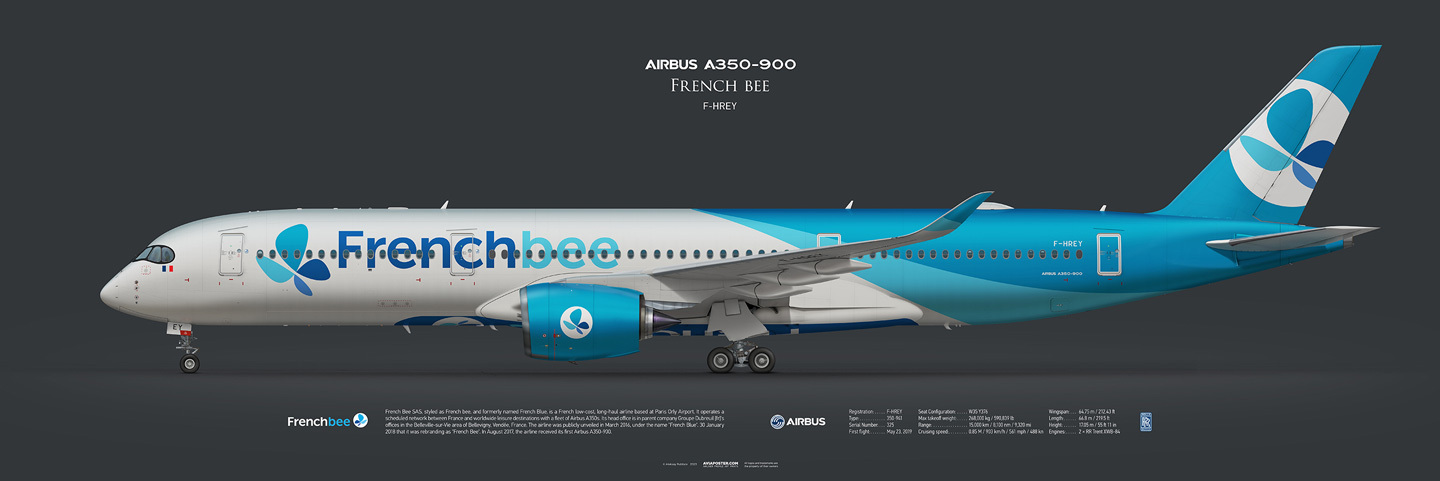
Digital Revolution
The Airbus A350 XWB isn’t just a pretty plane – it’s a flying tech lab, pushing avionics and systems to new heights. It’s packed with industry firsts that make it special. Here are some standouts onboard.
Integrated Modular Avionics (IMA) – Brain Evolution
The A350 borrowed the IMA concept from the A380 but cranked it up. While the A380’s IMA ran 23 functions, the A350’s handles over 40 – oxygen systems, full cabin pressure control, fire detection, you name it. It’s the first time so many systems linked into one network via Avionics Full-Duplex Switched Ethernet (AFDX) at 100 Mbps. This slashed processor and module counts by 50% over old-school setups – less power, less weight, easier upkeep, higher reliability. It’s like the plane’s brain got smaller but sharper.
Cockpit
The A350’s cockpit ditched the A380’s giant screen for six 15-inch LCDs, two of them touch-enabled (an option 20 airlines picked by 2019). It’s the first time touchscreens hit standard controls in commercial aviation. Pilots can drag data between screens like on a tablet, simplifying tasks and paving the way for upgrades. Plus, the Electronic Flight Bag (EFB) is fully baked into the avionics – not just tacked on – a first.
SBAS as Standard
The A350 pioneered Satellite-Based Augmentation System (SBAS) as standard gear. This satellite correction boosts navigation precision, aiding landings in tricky conditions (like low visibility) and cutting reliance on ground-based ILS. Pre-A350, SBAS was rare; here, it’s built-in.
FORCE and Predictive Maintenance
The Airbus Flight Operational Real-time Analysis (FORCE) system is another first. It blends real-time data with predictive analytics to flag issues before they strike, halving "no-fault found" part removals versus the A380. No more guesswork – the plane tells techs what’s up.
Autonomous Flights: ATTOL
The 2020 Autonomous Taxi, Take-Off & Landing (ATTOL) project made the A350-1000 the first plane to nail fully autonomous takeoffs and landings using image recognition (no ILS). Cameras and algorithms replaced old systems – a leap for future automation. Tested on the A350, it’s rippling through the industry.
Doors and Slides Under Control
Diehl Aerospace’s Doors and Slides Control System (DSCS) is another first. It’s the first commercial plane where doors and emergency slides run on contactless electronic sensors – more reliable and lighter than mechanical setups.
The A350 dares to innovate. Touchscreens, expanded IMA, standard SBAS, predictive maintenance, and autonomy steps – these trailblazing moves others now follow. It doesn’t just fly; it thinks for the crew and engineers, setting aviation’s future tone. Tons more systems could claim "first" bragging rights, but only those who built it could tell the full tale.
The Airbus A350 XWB isn’t just a pretty plane – it’s a flying tech lab, pushing avionics and systems to new heights. It’s packed with industry firsts that make it special. Here are some standouts onboard.
Integrated Modular Avionics (IMA) – Brain Evolution
The A350 borrowed the IMA concept from the A380 but cranked it up. While the A380’s IMA ran 23 functions, the A350’s handles over 40 – oxygen systems, full cabin pressure control, fire detection, you name it. It’s the first time so many systems linked into one network via Avionics Full-Duplex Switched Ethernet (AFDX) at 100 Mbps. This slashed processor and module counts by 50% over old-school setups – less power, less weight, easier upkeep, higher reliability. It’s like the plane’s brain got smaller but sharper.
Cockpit
The A350’s cockpit ditched the A380’s giant screen for six 15-inch LCDs, two of them touch-enabled (an option 20 airlines picked by 2019). It’s the first time touchscreens hit standard controls in commercial aviation. Pilots can drag data between screens like on a tablet, simplifying tasks and paving the way for upgrades. Plus, the Electronic Flight Bag (EFB) is fully baked into the avionics – not just tacked on – a first.
SBAS as Standard
The A350 pioneered Satellite-Based Augmentation System (SBAS) as standard gear. This satellite correction boosts navigation precision, aiding landings in tricky conditions (like low visibility) and cutting reliance on ground-based ILS. Pre-A350, SBAS was rare; here, it’s built-in.
FORCE and Predictive Maintenance
The Airbus Flight Operational Real-time Analysis (FORCE) system is another first. It blends real-time data with predictive analytics to flag issues before they strike, halving "no-fault found" part removals versus the A380. No more guesswork – the plane tells techs what’s up.
Autonomous Flights: ATTOL
The 2020 Autonomous Taxi, Take-Off & Landing (ATTOL) project made the A350-1000 the first plane to nail fully autonomous takeoffs and landings using image recognition (no ILS). Cameras and algorithms replaced old systems – a leap for future automation. Tested on the A350, it’s rippling through the industry.
Doors and Slides Under Control
Diehl Aerospace’s Doors and Slides Control System (DSCS) is another first. It’s the first commercial plane where doors and emergency slides run on contactless electronic sensors – more reliable and lighter than mechanical setups.
The A350 dares to innovate. Touchscreens, expanded IMA, standard SBAS, predictive maintenance, and autonomy steps – these trailblazing moves others now follow. It doesn’t just fly; it thinks for the crew and engineers, setting aviation’s future tone. Tons more systems could claim "first" bragging rights, but only those who built it could tell the full tale.
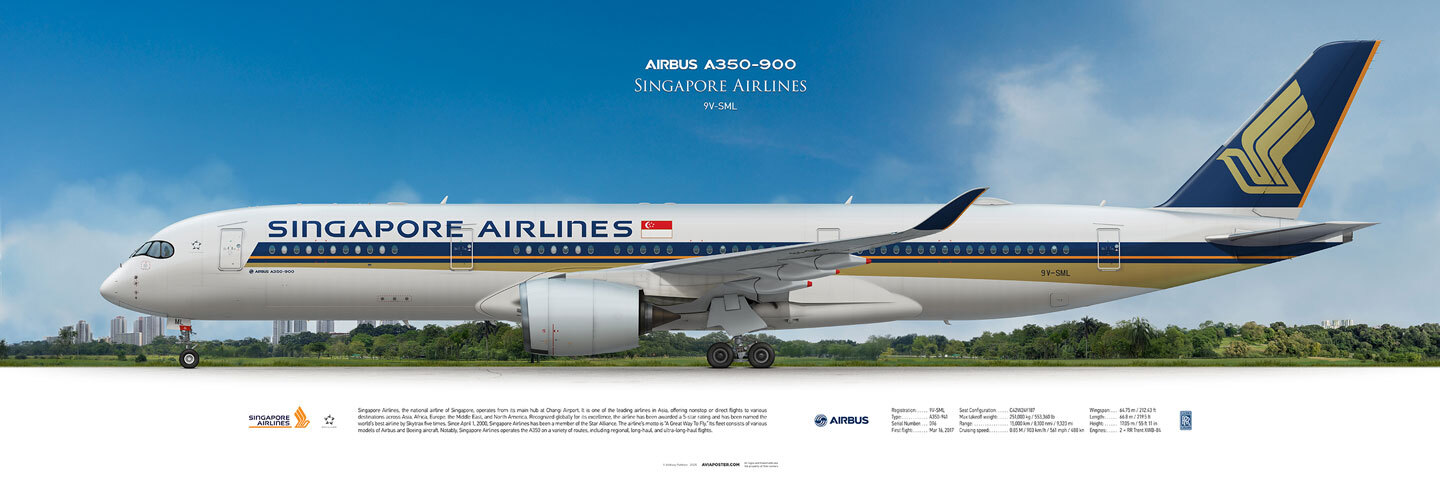
Ultra Long Range
The A350-900’s range hit 15,000 km – impressive, but customers wanted more, so Airbus engineers rolled up their sleeves. The A350-900ULR (Ultra Long Range) is a souped-up A350-900 built for extreme hauls. It can cover 18,000 km (about 9,700 nautical miles) without refueling, ranking it among the longest-range commercial planes out there. How’d they pull it off?
No extra fuel tanks here – ULR maxes out the existing ones. The central tank, partly unused in the standard version, now gets fully tapped, boosting fuel capacity to 165,000 liters – 24,000 more than the base model. This keeps the airframe unchanged and aerodynamics intact.
Cabin setup plays a role too. ULR configs often cut seats (161–170 versus 300+ in standard layouts), trimming payload for up to 20-hour flights. Passengers get more legroom and upgraded business/premium classes.
Singapore Airlines sparked the ULR’s creation for routes like Singapore to New York (about 15,300 km). Its first flight kicked off in 2018.
Otherwise, the ULR keeps the A350-900’s perks: composite fuselage, Trent XWB engines, top fuel efficiency, and low noise.
The A350-900’s range hit 15,000 km – impressive, but customers wanted more, so Airbus engineers rolled up their sleeves. The A350-900ULR (Ultra Long Range) is a souped-up A350-900 built for extreme hauls. It can cover 18,000 km (about 9,700 nautical miles) without refueling, ranking it among the longest-range commercial planes out there. How’d they pull it off?
No extra fuel tanks here – ULR maxes out the existing ones. The central tank, partly unused in the standard version, now gets fully tapped, boosting fuel capacity to 165,000 liters – 24,000 more than the base model. This keeps the airframe unchanged and aerodynamics intact.
Cabin setup plays a role too. ULR configs often cut seats (161–170 versus 300+ in standard layouts), trimming payload for up to 20-hour flights. Passengers get more legroom and upgraded business/premium classes.
Singapore Airlines sparked the ULR’s creation for routes like Singapore to New York (about 15,300 km). Its first flight kicked off in 2018.
Otherwise, the ULR keeps the A350-900’s perks: composite fuselage, Trent XWB engines, top fuel efficiency, and low noise.
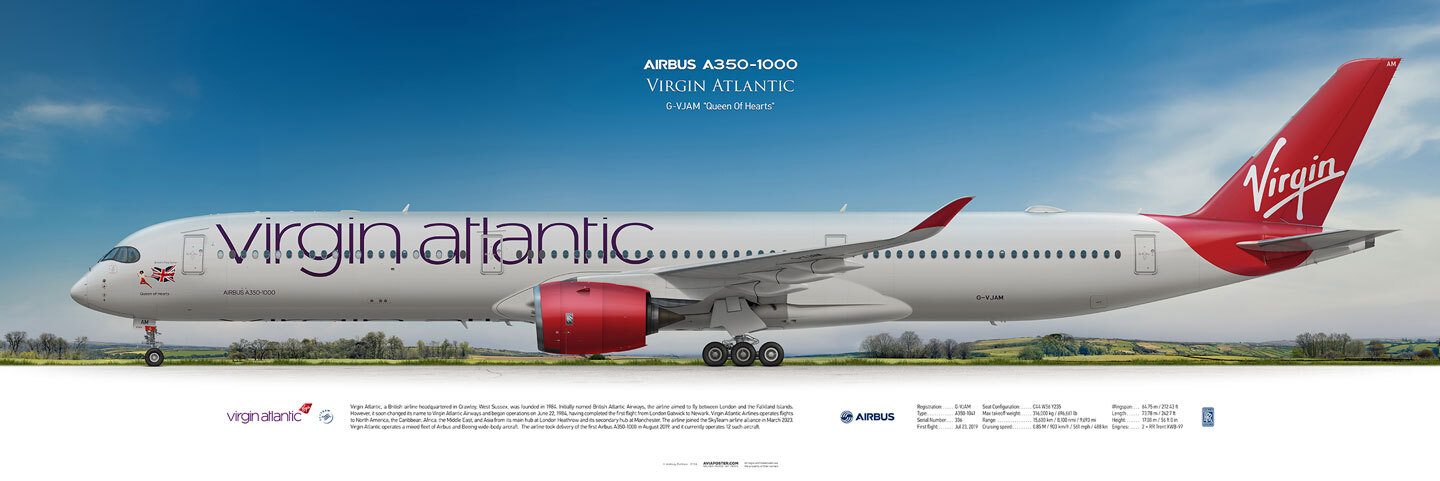
Epilogue
For aviation buffs, the A350 showcases how far plane-building has come. Composite airframes, adaptive wings, and next-gen engines aren’t just upgrades – they’re a leap to lighter, greener, stronger airliners. Carriers like Qatar Airways and Singapore Airlines push it on ultra-long routes, proving its real-world chops.
The A350 doesn’t just fly – it rewrites flight rules. Next time you spot it taxiing, remember: beneath that sleek shell lies a trove of cutting-edge tech.
For aviation buffs, the A350 showcases how far plane-building has come. Composite airframes, adaptive wings, and next-gen engines aren’t just upgrades – they’re a leap to lighter, greener, stronger airliners. Carriers like Qatar Airways and Singapore Airlines push it on ultra-long routes, proving its real-world chops.
The A350 doesn’t just fly – it rewrites flight rules. Next time you spot it taxiing, remember: beneath that sleek shell lies a trove of cutting-edge tech.